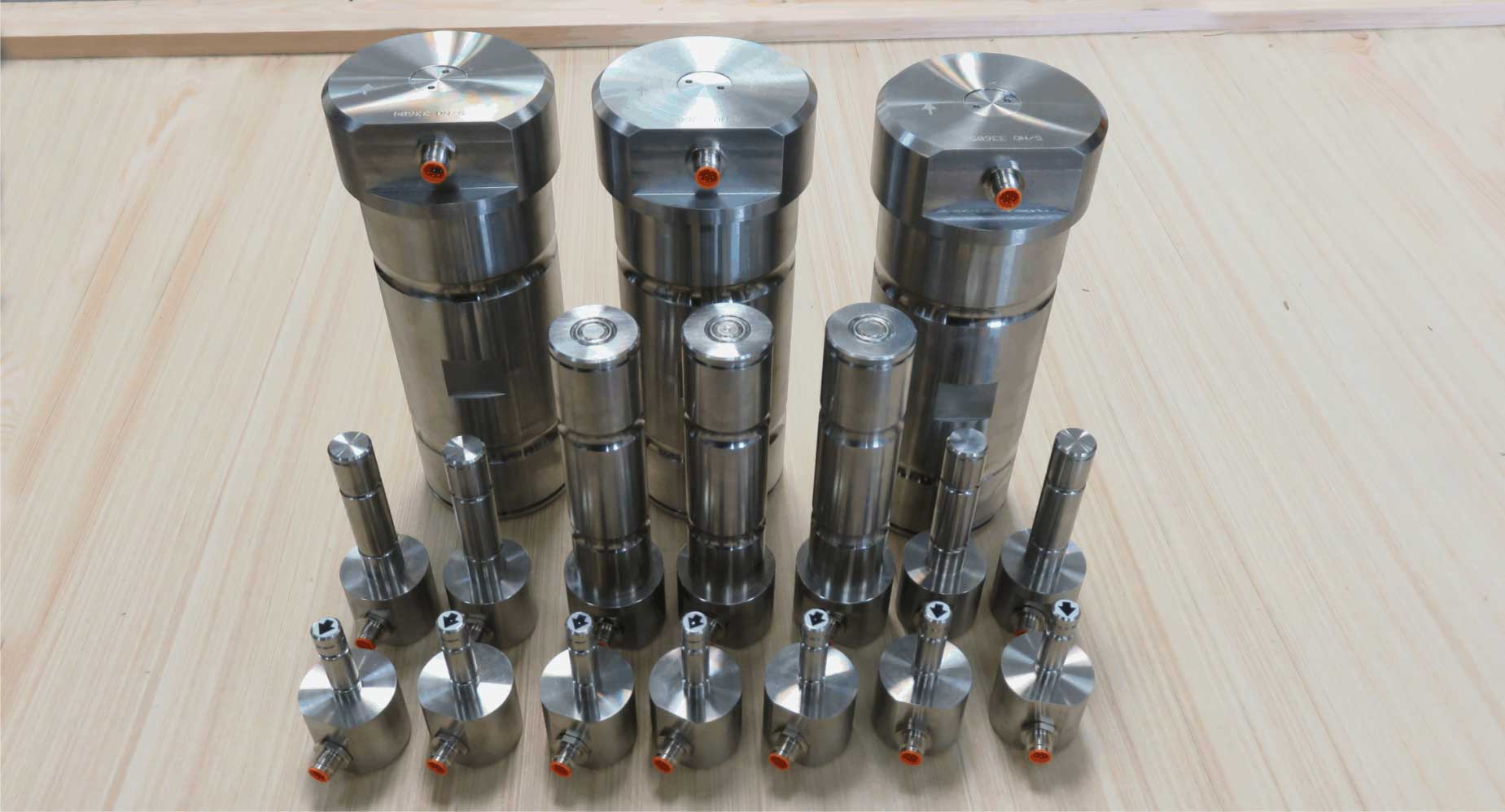
The Role of Load Cells in Aerospace Testing 📰
4th Jul 2024Aerospace testing demands precision, reliability, and safety to ensure the optimal performance of aircraft, spacecraft, and aerospace components. Load cells, with their ability to accurately measure forces and loads, play a critical role in various aerospace testing applications. This article explores the indispensable role of load cells in aerospace testing, including structural testing, flight testing, ground support equipment (GSE) testing, and payload verification.
Structural Testing:
Structural testing is essential for validating the integrity and performance of aerospace structures under various loading conditions. Load cells are extensively used in structural testing facilities to apply controlled loads and measure resulting strains, stresses, and deformations. Whether it's static testing to assess structural strength or fatigue testing to evaluate durability, load cells provide precise measurement capabilities, enabling engineers to verify designs, identify potential failure modes, and ensure compliance with safety standards.
Flight Testing:
Flight testing is a critical phase in aerospace development, allowing engineers to evaluate aircraft performance, stability, and control characteristics in real-world conditions. Load cells are integrated into flight test instrumentation to measure aerodynamic forces and moments experienced by the aircraft during flight manoeuvres. By accurately capturing lift, drag, thrust, and torque data, load cells provide valuable insights into aircraft behaviour, enabling engineers to refine designs, optimise performance, and validate flight control systems.
Ground Support Equipment (GSE) Testing:
Ground support equipment plays a crucial role in aerospace operations, supporting aircraft maintenance, servicing, and ground handling activities. Load cells are utilised in GSE testing to verify the performance and safety of equipment such as aircraft jacks, towbars, and lifting devices. Load cells measure loads exerted on GSE components during operation, ensuring structural integrity and preventing overloading or failure. Additionally, load cells facilitate load testing of aircraft cargo systems and restraint mechanisms to ensure secure transportation of payloads.
Payload Verification:
Payload verification is essential for ensuring the integrity and functionality of payloads such as satellites, scientific instruments, and cargo containers during launch and deployment. Load cells are employed in payload integration facilities to measure loads exerted on spacecraft and payload adapters during handling and transportation. By accurately monitoring loads, load cells verify payload compatibility with launch vehicles, assess structural integrity, and ensure proper distribution of forces during ascent and separation stages.
Conclusion:
In aerospace testing, where precision, reliability, and safety are paramount, load cells play a crucial role in validating structural integrity, evaluating aerodynamic performance, testing ground support equipment, and verifying payload compatibility. By providing accurate measurement of forces and loads, load cells enable engineers and researchers to make informed decisions, optimise designs, and ensure the success of aerospace missions. As aerospace technology continues to advance, the demand for advanced load cell solutions will remain integral to the ongoing innovation and improvement of aerospace systems and vehicles.